DUFLEX underlies New Generation Charter Cat
NEW Noosa Cruiser Incorporates DuFLEX Strip
DuFLEX the Key to Speed and Stability
ATL Composites has supplied DuFLEX Composite panels and KINETIX high performance epoxy systems for the latest designs from Norman R. Wright & Sons for two new custom designed Pilot Boats for PNG Ports Corporation.
“Siabo” is the first boat to hit the water from Wrights featuring their all-new Extra Long Waterline (XLW Class) design, which offers optimum seakeeping and efficiency in all sea conditions and speeds in excess of 30 knots.
Norman R. Wright & Sons was one of 10 companies to tender for the first of a fleet of 14.2-metre pilot craft.
The DuFLEX Building System was used for the entire vessel construction, including hull shell, frames, bulkheads, deck and superstructure. Panels were supplied as full-sized components and offered significant structural weight savings over infusion and other traditional methods, as well as eliminating the substantial costs associated with moulding.
Working with ATL Composites, Wright’s Naval Architects and Master Tradesmen integrated unique composite construction, combining resin-infused and pressed GRP cored panels with DNV-GL approval.
The design allows for a reduced centre of gravity for superior stability enhancing pilot safety when alongside ships, along with wide, flush, uninterrupted side decks around the entire vessel for optimum safety.
The two new boats are the first in what is expected to be a fleet catering to the growing ports, cargo and liquid natural gas infrastructure in Port Moresby and the 21 other surrounding PNG ports that they service.
PNG Ports Corporation visited Wright’s headquarters at Rivergate Marina & Shipyard, Brisbane and trialled a comparable vessel.
“They were impressed with our 110-year history, our factory and our history of support on similar fleets in North Queensland,” said Tony Riek, Managing Director.
The 14.2-metre design is customised specifically to the needs of PNG Ports Corp designs and is based on an evolution of Wrights’ highly successful Skirmish Class Pilot Boats which draw on over 80 years of Pilot Boat design and building expertise.
“Pilot Boats are a part of our DNA,” explained Tony. “We designed and built our first in 1935 and since then designed and built some of the sturdiest craft seen, in some of the harshest Australian waterways and beyond.
“The quality of our boats means many are still in continuous service after decades of operation. There are Pilot Boats still in operation which we built in 1993. We have a team of highly skilled and qualified naval architects and boat builders using the latest technology, processes and high-tech materials.”
ATL Composites engineered the vessel to meet DNV-GL: 1A HSLC R2 CREW, and worked closely with Adam Evripidou, Tony Riek and the Wrights’ team on developing and optimising build techniques.
DuFLEX Composite Panels reduce construction time and optimise structural weight in the production of light weight composite structures. Using DuFlex panels in boat construction avoids time-consuming laminating, coring and vacuum bagging steps normally required to fabricate high performance composites, and material waste, labour and tooling costs are greatly reduced
More information at www.duflex.com.au
Video of the boat in action: https://www.youtube.com/watch?v=g-ZpYgBPZ5A
Light, strong, fast and versatile, the Noosa 7 is turning heads and winning hearts.
Feature-filled power cat AYANA breaks New Ground in Charter
The latest Roger Hill-designed vessel, the 14-metre power catamaran called “AYANA”, has emerged from production at Noosa Marine and is now stored at The Boat Works, awaiting delivery to her discerning owners who plan to cruise from the Gold Coast back to their home waters of WA.
The fully-custom designed and built power cat is replete with unique features befitting a luxurious liveaboard vessel. With her planing hull, AYANA was built to survey with the intention of offering day charters cruising Rottnest, Margaret River and the Swan River.
As Julian Griffiths, Director at Noosa Marine explains: “AYANA weighs around 12.8 tonnes and has loads of extras. Her owner is an experienced boatie and wanted the works.”

AYANA is a spacious three-cabin multihull conceived for day charter, with a massive, versatile cockpit for entertaining or angling, which flows into the large saloon, also decked out for socialising with dinette, galley, AV and large windows for panoramic views. The enclosed flybridge features the helm and an L-shaped lounge and dining table, while the aft deck is fitted with a davit for the vessel’s tender.
Designer Roger Hill said the list of ‘must haves’ was daunting for him as a designer and for the team at Noosa Marine.
“From my perspective, the challenges involved weight control more than anything else. AYANA is a 14-metre superyacht. It probably has more fridges and freezers than any other 14-metre afloat!
“There is no such thing as a boat that is not some form of resolved compromise. But this boat is probably as close to what the owners would say has everything they want in a 14-metre package and from my point of view the biggest compromise will be the performance of the planing hull, which will still achieve around 28 knots.”
According to Roger, building to survey requires more structural material and more safety details, which results in extra weight and additional costs of around 20 percent.
“This boat was built to the highest standard of survey in Australia so it is at the top end of the spectrum for cost and compliance,” adds Roger.
From briefing to completion, construction took just 13 months. The Noosa Marine production team comprised Julian, Max, two apprentices and a labourer.
Key to their efficiency was the use of the pre-cut DuFLEX panel system from ATL Composites.
Other DuFlex panels in AYANA were cored with Divinycell’s H80, an industry standard for marine projects and ATL’s Featherlight Marine Interior panels combined Divinycell H60 core with 600gm double bias laminates.
All components for the build, from temporary framing to structural hull sections, bulkheads through to the interior fit-out for AYANA were digitised from design files and nested to optimise the number of panels required for the project that were with ATL’s proprietary Z-Joint for joining and subsequent quick assembly.
“DuFLEX is incredible for saving time and reducing weight onboard,” Julian attests. “DuFlex offers builders a very high-quality panel and very precise accuracy, and for the client, an assurance of structural integrity.”
Roger agrees, stating: “Using the ATL Composites DuFlex panel system is a great way to build a boat particularly when it is embraced so well by this builder. Personally, I really appreciate the service and help that the team at ATL offers me as a designer. Their back-up and support are great.”
Breathing Life Into Boats
ATL Composites provides the precision pieces for the latest Roger Hill-designed powercat.
From concept to completion, building a custom-designed powercat is a breeze with an inspired vision, reliable team, proven materials and just a pinch of magic in the mix.
The product of her owners’ yachting experience and dream of long-range cruising, “Omahu”, a 16-metre composite displacement hull powercat from the pen of legendary designer, Roger Hill, is taking shape at Lifestyle Yachts in Pipiroa, New Zealand.
Meaning “breath”, or “light breeze” in the Maori language, Omahu is a custom-designed vessel that is unique in every aspect.
As Roger Hill explains “The hull shape is a development of our very efficient displacement form, but the styling is unique compared to other similar sized power cats we have done before. It is not a ‘cut and shut’ exercise using an existing similar sized design.”
Omahu is the vision of joint-owners, two Kiwi couples keen to experience long-range cruising around the South Pacific, exploring New Caledonia, Fiji, Tonga and Australia.
One of the owners had previously built a Roger Hill-designed 14.15-metre sailing cat, around 15 years ago, customised to his requirements at that time. The choice of building materials, methodology and designer informed his choice for the current project.
According to Roger, the brief was reasonably straight forward. “There were around 20 specific items”.
“Both owners are very experienced yachtsmen, in power and sailing boats, with ocean-going range as the primary requirement. Both are very practical people, so it wasn’t difficult to convert their thoughts and ideas into the design.”
Emphasis was on comfort, rather than speed, although, powered by twin Yanmar 6LY400 400hp engines, Omahu is calculated to achieve an impressive top speed of 26 knots.
The design needed space for two couples to live aboard along with storage required for long trips to remote destinations where fuel, water and food might not be readily available.
“One of the interesting things that came up right at the start was how big the vessel should be. After some discussion, I suggested that perhaps they should go and find a suitable marina berth to keep it in, and that’s what happened. From that point, we worked out the maximum beam and a maximum length.”
The design process involved relatively few challenges.
“You have probably heard about the ‘design spiral’, the process of starting with a ‘loose’ collection of info and data and compromise through the design journey this becomes tighter and tighter until the final result is signed off.
The result of their collaboration will be a sensational wide-bodied powercat that embodies the “space, pace and grace”, the characteristics of multihulls that inspire such loyalty in their owners.
“This particular design does not have as much beam (5.6-metres) as I might normally have on a displacement power cat of this length, but this was related to the width of the marina berth. The upside of that slightly narrower beam, less transverse stability will be an improved motion; not such a quick roll period in a beam sea.”
With her shallow draft of just over 1-metre, Omahu will be able to explore remote inlets and anchorages where other yachts may not be able to access.
Seeking strength, durability, light-weight and precision, Roger based the design of Omahu on construction using DuFLEX Composite panels from ATL Composites.
“ATL and I go back a long way,” recalls Roger. “The first DuFLEX kit we did was over 18 years ago, and we have done many since then in both power and sail. One of Omahu’s owners had already built a sailing cat using the DuFLEX panel system so he was very happy to build the power cat using the same materials and method of construction.
“Another consideration was the builder, who didn’t have a lot of experience building a full-foam cored catamaran, so he has been very appreciative of the pre-made panels and CNC router set of parts.
“The DuFLEX Building System offers builders a very high-quality panel and very precise accuracy, and for the client, an assurance of structural integrity.”
From a technical standpoint, Omahu is destined to have a dark blue hull which dictated the choice of foam core to be used in the hull and transom areas. A combination of Divinycell HP80 and HP100 foam cores, type approved by DNV-GL Maritime, were chosen for the DuFLEX Strip Planks used in these areas to provide elevated temperature and mechanical performance under the owners’ choice of a dark blue paint.
Engineered to survey standards by ATL Composites Engineering team, other DuFLEX Composite Panels components in Omahu include wing-deck, soles, girders, webs, bulkheads, longitudinal and interiors all supplied in CNC-Routed Kit Form with various core types and densities to suit the design loads in the vessel.
Far from handing over the plans and moving on to the next commission, Roger Hill prefers to work closely with clients and yard as the vessel is brought to life.
“I really enjoy the developing relationship between the client, the builder and myself. It’s tremendous when the builder is on song and going well, the client is seeing his new boat taking shape and I get involved with helping in any way I can to make the process go as smooth as possible.
“Being a designer must be one of the more satisfying things to do on the planet and that probably applies to just about designing anything. But boats, I think are a little bit more special, it is such a complex sum of all of its parts and then when done well become much more than the sum of its parts.”
ATL Composites’ Expertise & Experience Underlie The Whiskey Project
The highlight of the recent Pacific 2019 Expo at Sydney’s Darling Harbour, the intriguingly named “Whiskey Project”, stole the spotlight with the launch of its first boat – WHISKEY ALPHA eight five – and won a legion of fans for its aggressive profile, versatility and performance capabilities.
Built by Van Munster Boats, located on Lake Macquarie in NSW, Whiskey Alpha eight five is the first “Next Generation Tactical Watercraft”, the product of collaboration among exmilitary operators, world-class maritime architects, engineers and innovators.
The “Whiskey” nomenclature is derived from the NATO phonetic alphabet where “W” denotes the military water operators and “Whiskey” is their callsign. Whiskey Alpha eight five is 8.5m long but is scalable from 6 to 12-metres.
Featuring a new-technology hull that boat builder Brett Van Munster describes as ‘disruptive’, the high-performance powerboat hull is made from advanced carbon fibre composite materials which provide a greater strength to weight than traditional aluminium or FRP hulls.
The revolutionary Sea Blade hull form is the product of a decade of research and development to design the ultimate foundation for mixed sea states and offshore applications providing greater stability and seakeeping whilst achieves a higher average speed than a comparable deep-V hull.
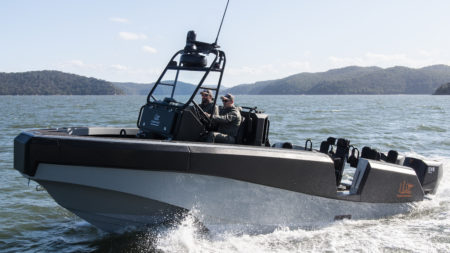
As Brett Van Munster explains “The co-founders of The Whiskey Project commissioned the design based on their 20 years’ Defence experience as tactical maritime operators, and they intimately understood what the capability gaps were in the existing craft being used globally.
“They knew the current boats were simply not fit for purpose. Whether they are from military or police or other state agencies or even support boats or tenders, operators need watercraft that offered a higher level of seakeeping and safety but also high-speed offshore capability in all sea states as well as low speed manoeuvring for the boarding, recovery or disembarking of ships.
“These vessels needed to offer an unprecedented level of stability and high-end performance!”
The Whiskey co-founders, Darren Schuback and Ryan Carmichael assembled a formidable design and build team which included the lead architect from Farr Yacht Design; marine composites engineer and America’s Cup winner Brett Ellis, as well as Computational Fluid Dynamics (CFD) system and hull specialists from Navatek Hawaii, a research institute funded by the US Government to build military craft.
“Darren and Ryan were really motivated. They had the financial backing and a clear conceptual design brief when they approached us.”
With a similar ethos, Van Munster boats, established in 1988, is a second-generation familyowned and run business that has earned a reputation for innovative custom builds. Their “bread and butter” is 18 and 16-foot skiffs, for which they’ve been the international Class\ builder for the past 14 years.
“The reason we established the business was that we couldn’t find what we wanted in the market. We were seeking better technical construction in our boats, and that’s what we strive to achieve in our boats every time.”
Specialists in custom composite construction, Van Munster Boats had a clear build and test deadline for The Whiskey Project boat of the 2019 Pacific Maritime Expo.
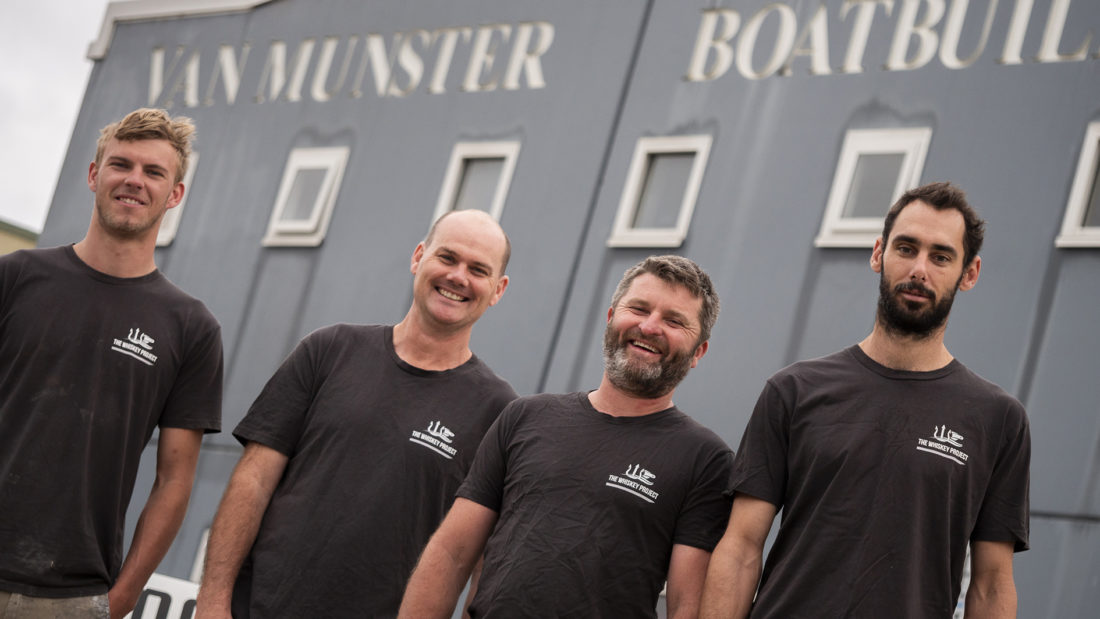
“The timelines are never as long as you’d like them to be,” says Brett. “But we specialise in race boats, so we’re used to the environment of high performance and high expectations. That’s the culture of our business and how we operate. But it was a good challenge. There was no fallback, no wiggle room. The whole thing had an end date. It was a like a race from the start to the finish and we delivered.
“One of the key challenges that always arise on tight time frames is material procurement. Fortunately, we have good suppliers such as ATL that we can rely on to deliver. You can’t do this kind of project by yourself.”
Nicholas Cossich, Director at ATL Composites said the smooth process from brief to completion on the Whiskey Project was testament to the strong relationship between ATL and Van Munster Boats.
“It’s an immense privilege for us to work with such a dynamic and supremely talented group of people operating at the highest echelons of the marine industry. Brett and his team really demonstrated true ingenuity and focus in delivering the WA85 and we are very proud that he chose to use our Australian technology to deliver such a ground-breaking vessel.”
For two decades, Van Munster Boats has worked with ATL Composites on numerous projects ranging from classic timber construction in the early days, through to the high performance, advanced composite boats they’re renowned for now.
For The Whiskey Project, ATL Composites supplied Divinycell foam core to deliver the high strength structure required in such extreme operating conditions, and fast speeds, and custom DuFLEX panels for deck, cockpit and internal framing. ATL CNC machined components to the uniquely engineered requirements “and we just dropped them into the
boat” added Brett.
The Whiskey Project lead engineer Brett Ellis has been a friend and colleague of Brett Van Munster for decades and proved an invaluable part of the team, bringing his depth of experience as a structural engineer specialising in composites for Gurit, as well as Prada, Alinghi and Artemis.
The effort paid off and Whiskey Alpha eight five was the centre of attention at Pacific 2019, the biennial international maritime expo that attracts 22,000 visitors over three days, representing Defence, Government and Scientific industries from 48 nations.
“It was awesome for us to see the reception,” said Brett. “The Whiskey Project was the star of Pacific 19 and the Australian Defence Force all know about this vessel now!
“It was a whole new world and a real eye-opener for us as a niche business. We were very proud to demonstrate that we have the skillset, capabilities and craftsmanship that create a world-class product.
“There has been huge interest following the event from both domestic and international defence delegations as well as other government agencies and we are looking forward to the next phase of The Whiskey Project.”
MEET THE TEAM BEHIND THE WHISKEY PROJECT | Next up is Brett Van Munster, our Boat Builder
MEET THE TEAM BEHIND THE WHISKEY PROJECT | Next up is Brett Van Munster, our Boat Builder.
Posted by The Whiskey Project on Sunday, November 3, 2019
DuFLEX Composite Panels Saved Time and Weight
In terms of quality and innovation the new flagship of the shipping company Luzern (SGV) MS 2017 sets a new milestone in Swiss shipping.
March 21st 2017
In autumn 2013, the Board of Directors of the SGV decided on construction of the new, large passenger ship with space for 1,000 passengers.
The well-known yachting design office Judel / Vrolijk & Co from Bremerhaven were commissioned to do the design, and the planning and construction is being carried out by Shiptec AG, one of the largest shipyards in Switzerland.
A new sundeck floor was specified for the upper section of the vessel and vdL Composites GmbH were approached to supply a composite alternative to provide strength, stiffness and durability. DuFLEX Composite Panels were specified as the best option for the large 275m2 area.
DuFLEX – Optimised Kit Technology – 109 Custom DuFLEX panels ranging from 1.3m to 2.4m in length were manufactured at the vdL Composites facility in Wesel, Germany. The panels were cored with 60mm Divinycell H80 and reinforced with multiple layers of multiaxial E-fibreglass, laminated with a custom-blend, high performance epoxy resin. Divinycell H80 is widely used, and has a proven track record, in the marine industry for leisure, military and commercial applications. Combined with epoxy laminates, the DuFLEX H80 panels provide excellent mechanical properties at low weight, a consistent high quality finish, excellent chemical resistance, low water absorption and good thermal/acoustic insulation.
The panel edges were machined with the DuFLEX Z-Joint and CNC-routed from electronic design files, enabling the panels to be joined and the full-sized parts to be released. The panels were delivered, along with the proprietary DuFLEX Z-Press, to Shiptec to be joined and fitted on site. The Z-Press was set-up on the deck of the vessel, and vdL staff were present to assist with joining and to offer technical support during the process.
On installation, the full-sized parts fitted perfectly into the specified areas eliminating the need for time- consuming trimming and fitting. The large sections were lifted into position with a vacuum lifter and Pro-Set Epoxy adhesive was used to fill and bond non-scarffed edges. Multiaxial E-fibreglass tapes were applied to complete the structural requirements on those joins.
A driving factor in the choice of materials for this project was the installation time-frame. DuFLEX offered the perfect solution to meet a tight deadline for project completion.
The first contact was made to vdL on February 2 2016, with the first delivery on March 11. The first panels were joined on March 21 and 3 days later, one third of the deck was joined and mounted on the steel frame. 166 parts were installed to complete the 275m2 deck. Compared to conventional methods of hand-lamination, this saved hours in labour, wastage and tooling costs.
MS 2017’s maiden voyage is scheduled for May 2017. The ship will be officially named at this time and will be scheduled for trips on the Lucerne-Flüelen-Luzern and Lake Lucerne.